Our Alcast Company Statements
Our Alcast Company Statements
Blog Article
All about Alcast Company
Table of Contents8 Easy Facts About Alcast Company ShownSee This Report about Alcast CompanySome Of Alcast CompanyWhat Does Alcast Company Mean?The smart Trick of Alcast Company That Nobody is DiscussingNot known Incorrect Statements About Alcast Company The 8-Second Trick For Alcast CompanySome Of Alcast Company
It had excellent strength and machinability. There are lots of other aluminum alloys that can be used for casting components. To locate out which alloys would certainly be good for your projects, get in touch with Impro.
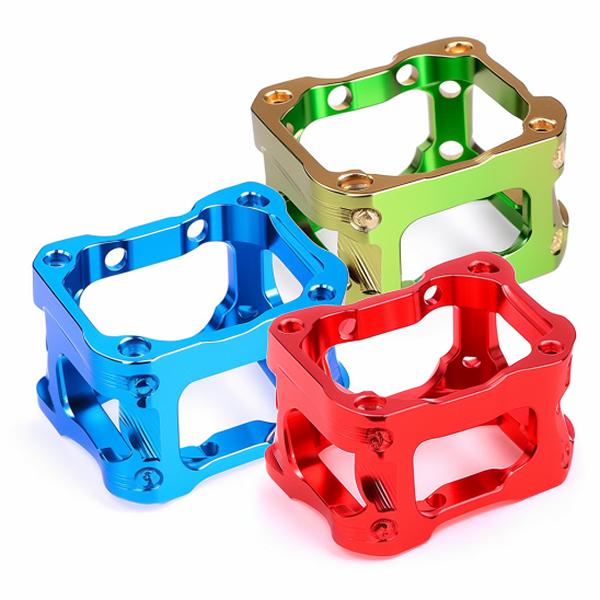
Various elements and quantities create a wide range of desirable physical and chemical residential properties. And the Aluminum Association (AA), based in The United States and copyright, has actually produced requirements that regulate light weight aluminum alloys' structure, homes, and nomenclature. There are two sorts of aluminum alloys functioned and cast. Factory employees develop these alloy key ins various methods, which substantially impacts their attributes.
The Ultimate Guide To Alcast Company
Cast aluminum alloys are made by melting pure aluminum and incorporating it with other metals while in fluid kind. After that the mix is put right into a sand, die, or investment mold. After solidification, the steel is gotten rid of from its mold and mildew. At this stage, it remains in either its last kind or as a billet or ingot for further processing.
There are many small differences in between wrought and cast light weight aluminum alloys, such as that actors alloys can include a lot more considerable amounts of various other metals than wrought alloys. The most notable difference between these alloys is the construction procedure via which they will certainly go to deliver the last item. Apart from some surface therapies, cast alloys will exit their mold and mildew in nearly the exact solid kind wanted, whereas functioned alloys will undergo several alterations while in their solid state
A Biased View of Alcast Company
If you think that a functioned alloy may be the very best for your task, have a look at several of our articles that describe even more about details wrought alloys, such as Alloy 6061 and Alloy 6063. On the various other hand, if you think a cast alloy would certainly be much better for you, you can find out extra about some cast alloys in our Alloy 380 and Alloy 383 write-ups (coming quickly).
When picking an aluminum foundry for your manufacturing demands, it's essential to examine a number of elements. Among one of the most explanation critical elements to take into consideration is the experience and skills of the shop. Choosing a foundry that has the appropriate understanding of the light weight aluminum spreading process, and the portfolio to show for it, helps to have a successful end result for your task.
How Alcast Company can Save You Time, Stress, and Money.
Having the experience and market knowledge to craft your castings for optimum manufacturing and quality end results will improve the project. Producing light weight aluminum spreading needs a complicated collection of processes to attain the ideal results. When selecting a brand-new light weight aluminum factory to partner with, guarantee they have comprehensive sector experience and are well-informed about all facets of the aluminum casting procedure: layout, manufacturing, material analysis, and product screening.
The factory ought to also have a proven performance history of supplying extraordinary items that satisfy or exceed consumer expectations. Quality control needs to also be at the top of your listing when choosing a light weight aluminum foundry. By collaborating with a qualified shop that follows the requirements for quality assurance, you can shield the honesty of your item and guarantee it meets your requirements.
Alcast Company - Truths
By selecting a business who offers services that satisfy or exceed your product requirements, you can be sure that your project will certainly be finished with the utmost accuracy and effectiveness. Particular light weight aluminum foundries concentrate on certain types of making processes or casting approaches. Various components require various manufacturing techniques to cast light weight aluminum, such as sand casting or pass away spreading.
Die casting is the name given to the procedure of producing complicated metal components through use of molds of the component, also understood as dies. It generates more components than any kind of various other procedure, with a high level of precision and repeatability. There are three sub-processes that drop under the classification of die spreading: gravity pass away casting (or long-term mold casting), low-pressure die spreading and high-pressure die casting.
Alcast Company Can Be Fun For Anyone
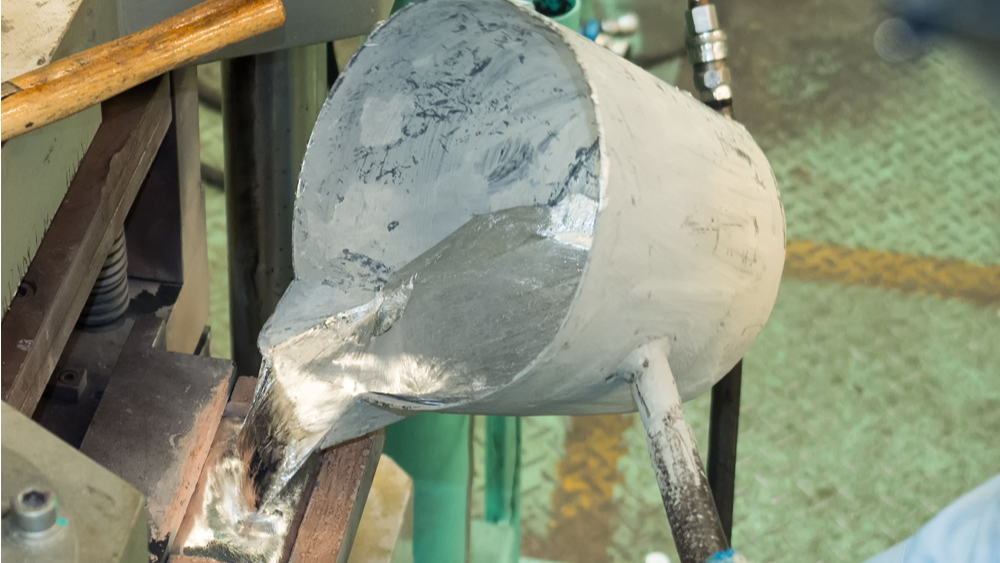
The pure metal, additionally called ingot, is included in the heater and maintained the molten temperature level of the metal, which is then transferred to the shot chamber and infused right into the die. The pressure is after that kept as the steel strengthens. Once the steel strengthens, the cooling process starts.
The thicker the wall surface of the part, the longer the cooling time as a result of the quantity of interior metal that additionally requires to cool down. After the component is fully cooled, the die halves open and an ejection system pushes the element out. Adhering to the ejection, the die is shut for the next shot cycle.
The 7-Minute Rule for Alcast Company
The flash is the additional material that is cast throughout the process. Deburring eliminates the smaller sized pieces, called burrs, after the trimming process.
Today, top producers utilize x-ray screening to see the entire inside of elements without reducing into them. To get to the finished product, there are 3 primary alloys utilized as die casting product to pick from: zinc, light weight aluminum and magnesium.
Zinc is one of the most pre-owned alloys for die spreading due to its lower expense of raw materials. Its deterioration resistance also enables the components to be long long-term, and it is one of the extra castable alloys due to its reduced melting factor.
The 25-Second Trick For Alcast Company
As stated, this alloy is just one of the most commonly used, yet makes will, at times, pick aluminum over zinc as a result of light weight aluminum's production benefits. Aluminum is highly affordable and among the extra versatile alloys. Aluminum is made use of for a variety of different items and markets anything from home window frameworks to aerospace products.
Report this page